“Vibration Hurts. Awareness Helps.”
HAVS (Hand-Arm Vibration Syndrome)
Training Course
Protecting Hands, Preserving Health
This Hand-Arm Vibration Syndrome (HAVS) Awareness Training course focuses on the risks associated with using vibrating tools and machinery in the workplace—and how to manage those risks effectively to prevent long-term harm.
HAVS is a serious and often permanent condition caused by regular exposure to vibration through tools such as grinders, chainsaws, impact drills, and high-torque wrenches, or by holding components being processed by powered machines. Left unmanaged, it can lead to numbness, loss of grip strength, and even permanent disability.
This course provides a clear understanding of:
• What HAVS is and how it develops. - The types of equipment and tasks that carry the highest risk
• The health hazards linked to prolonged vibration exposure
• How to conduct a vibration risk assessment
• Practical control measures to limit exposure and protect workers
What You’ll Learn
By the end of this course, you will be able to:
Understand the health risks caused by high levels of vibration exposure, including Hand-Arm Vibration Syndrome (HAVS)
Recognise the legal responsibilities of both employers and employees under the Control of Vibration at Work Regulations 2005
Carry out or contribute to a workplace vibration risk assessment
Understand how vibration levels are measured and how to avoid, reduce, or control exposure
Know when and how to use PPE effectively, and how to maintain and store it properly
Identify when health surveillance is required and who may be at greater risk
This course equips you with the knowledge to take practical steps in reducing vibration hazards and protecting long-term worker health.
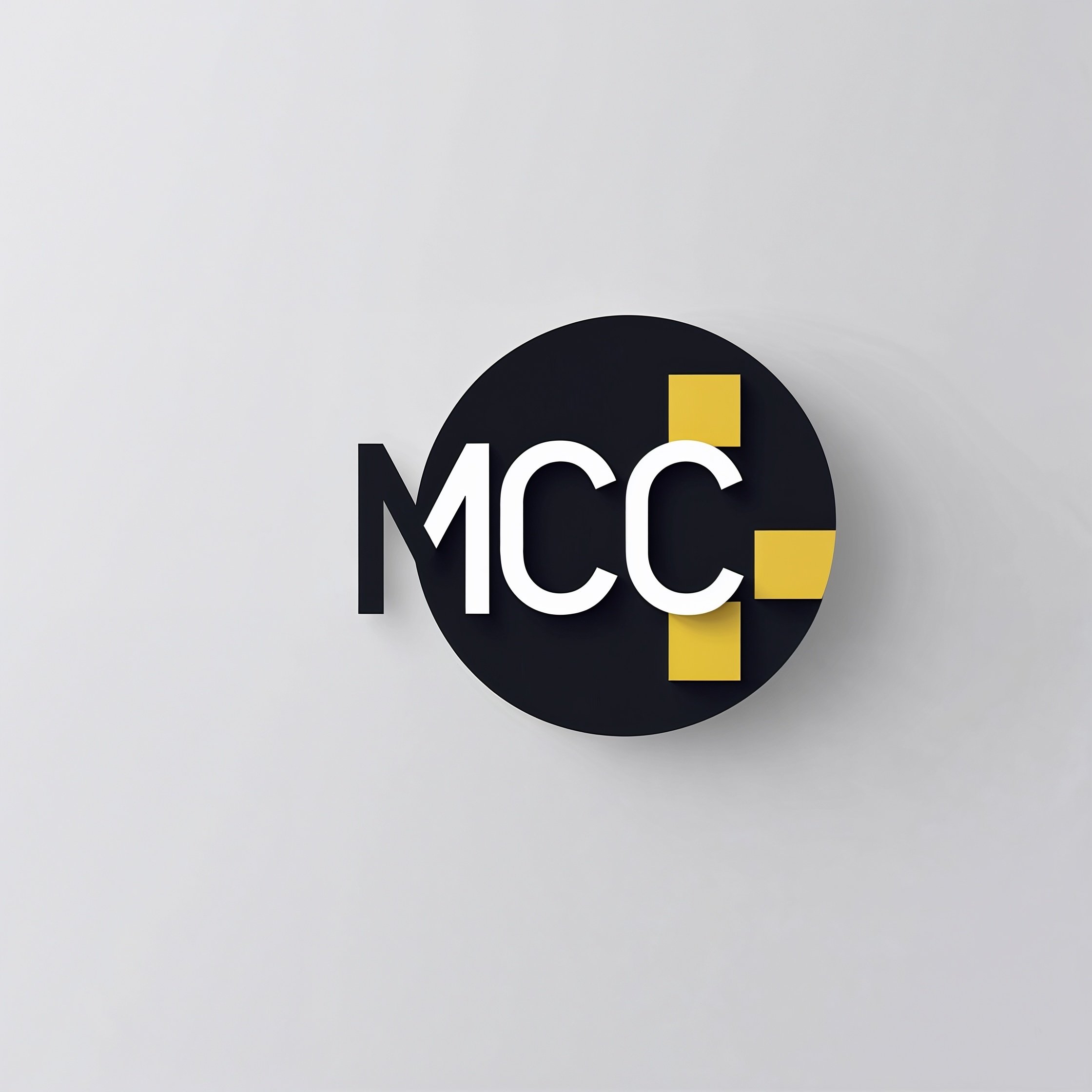
How it works….
On the course
At a glance…
6 - 12 delegates
Half day course
No qualifications or PPE required
This training course is delivered on-site at your location or at a training centre location and typically lasts half a day, No formal qualifications are needed to attend, making it accessible to all experience levels. Group sizes are kept small, usually between 6–12 delegates, to ensure focused, hands-on learning. Delegates are not required to bring any PPE for this training course
Module 1: Introduction to HAVS
This module provides a comprehensive introduction to Hand-Arm Vibration Syndrome (HAVS)—a serious, often irreversible condition caused by prolonged exposure to vibration. Learners will gain a clear understanding of what hand-arm vibration is, how it affects the body, and the early symptoms to look out for, such as tingling, numbness, and reduced grip strength.
We explore the industries most at risk, including construction, manufacturing, forestry, and utilities, and examine common vibrating tools and equipment such as grinders, chainsaws, breakers, and impact wrenches.
The module also outlines the legal framework that underpins vibration safety, including:
• The Control of Vibration at Work Regulations 2005
• The Health and Safety at Work etc. Act 1974
• The Supply of Machinery (Safety) Regulations 2008
Learners will be introduced to key terms such as Exposure Action Values (EAV) and Exposure Limit Values (ELV), helping them understand how vibration levels are measured and managed in the workplace.
Finally, the module touches on related risks, including noise exposure, and outlines the duties of both employers and employees in preventing HAVS and maintaining a safe working environment.
Module 2: Risk Assessment
Understanding how to assess and manage risk is essential in preventing vibration-related harm. This module breaks down the risk assessment process into clear, practical steps, giving learners the tools to identify and control vibration hazards effectively.
It begins by explaining key terms and what a risk assessment is, followed by who is responsible for carrying one out. Learners are guided through the five essential steps:
1. Identifying hazards – recognising equipment, tasks, and environments that could cause harm
2. Determining who might be harmed and how – focusing on individuals or groups most at risk
3. Evaluating the risks – assessing severity and likelihood, and applying the hierarchy of control to select appropriate measures
4. Recording the findings – documenting the process clearly and accurately to meet legal and organisational requirements
5. Reviewing and updating – ensuring risk assessments remain relevant as tools, tasks, or conditions change
By the end of this module, learners will understand how to approach vibration-related risk assessments with confidence and contribute to a safer, more compliant workplace.
Module 3: Reducing and Controlling Risks
This module focuses on practical strategies for managing and minimising vibration exposure in the workplace. Learners will explore a range of control measures, from equipment selection to health surveillance, designed to protect workers and meet legal responsibilities.
We begin by looking at purchasing and hiring policies, highlighting the importance of selecting low-vibration tools and ensuring manufacturers and suppliers provide accurate safety information and guidance.
The module then introduces the hierarchy of control, outlining key steps to reduce risk:
• Elimination – removing the vibration hazard entirely where possible
• Substitution – replacing high-vibration tools with safer alternatives
• Engineering controls – using design features, damping systems, or automation to reduce exposure
• Maintenance and inspection – ensuring tools are in good condition through regular checks, supported by a practical maintenance checklist
• Administrative controls – limiting exposure time, rotating tasks, and implementing safe systems of work
• Information, instruction, and training – making sure employees understand how to use equipment safely and follow best practice
The module also reinforces employee responsibilities, covering PPE where appropriate and the use of gloves, anti-vibration materials, and other protective equipment.
Finally, learners will gain an understanding of health surveillance—why it’s crucial, how it helps detect early signs of HAVS, and what employers must do to monitor and support affected workers.
By the end of this module, participants will have a comprehensive understanding of how to apply layered controls to manage vibration risks effectively and protect long-term worker health.
This HAVS training course is suitable for anyone who has responsibility for managing the risks of vibration in the workplace, as well as anyone who uses vibrating equipment or tools, or holds components being worked on by machinery, as part of their job role.
This includes those working in:
Construction and carpentry.
Mining, quarrying and stone masonry.
Forestry, estate management and grounds maintenance.
Foundries.
The public utilities sector (gas, electricity, water, etc.).
Engineering factories and workshops.
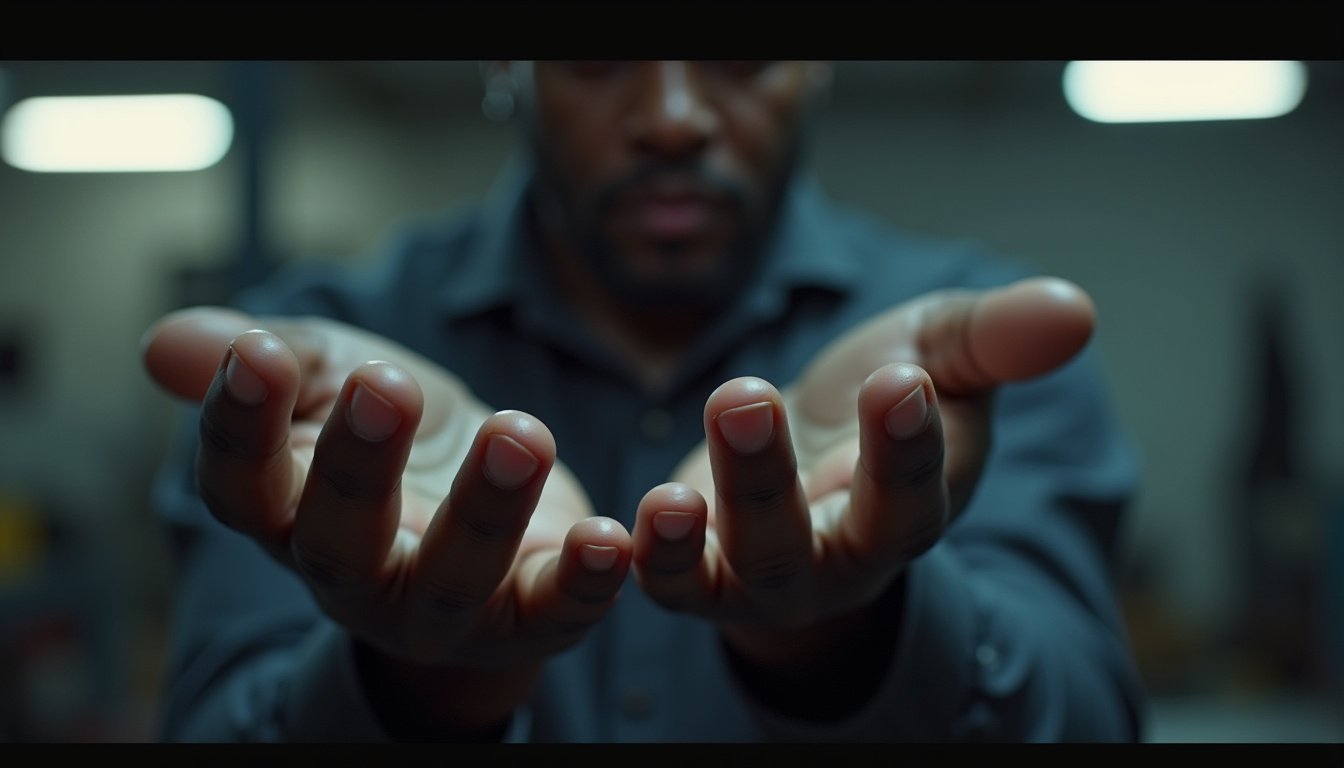